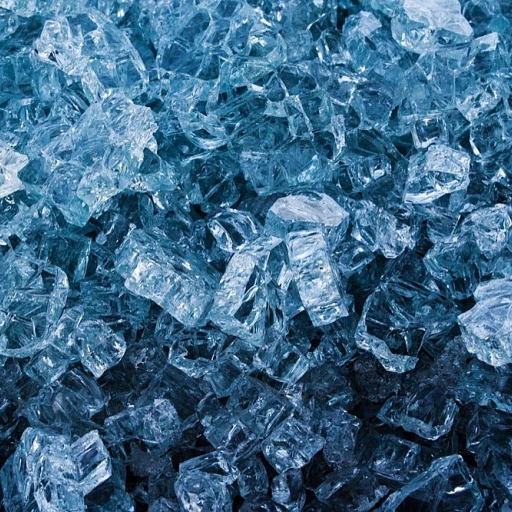
Common Reasons Your GE Profile Ice Maker May Stop Working
Understanding Why Your Ice Maker Might Stop
It's frustrating to discover your GE Profile ice maker has suddenly stopped producing ice. There are several common reasons this could happen. Here's what you need to consider:
- Power Supply Issues: Your ice maker's power supply is crucial. If there's a disruption, it can bring ice production to a halt. Pay close attention to the control board and make sure all connections are secure.
- Water Supply Disruptions: Ice makers need a steady flow of water. A clogged water filter or a malfunctioning water inlet valve can stop the ice-making process. It's vital to check your water supply lines for any kinks or blockages.
- Temperature Problems: The refrigerator freezer's temperature plays a role in ice production. If the freezer is too warm, the ice maker will struggle to produce ice cubes.
- Mechanical Malfunctions: Parts like the ice bin, ice maker motor, and components within the appliance could fail. Regular checks can help identify such problems early.
These common issues can often be resolved without professional appliance repair. However, some cases require expert intervention. It's important to know when you might need to schedule service with a trained technician.
For more in-depth troubleshooting steps, you might find this guide to troubleshooting ice makers helpful.
How to Check and Fix Power Supply Issues
Ensuring Proper Power for Your Ice Maker
A sudden stop in your GE Profile Ice Maker's functionality might be linked to power supply issues. It's crucial to first check the power connection to ensure your appliance is receiving electricity. Verify that your ice maker is plugged in securely and that the outlet is functioning correctly. You can test this by plugging a different appliance into the same outlet.
- Inspect the Control Board: The control board acts as the brain of your ice maker. If it's malfunctioning, it may prevent the ice maker from working. Look for any visible damage or burnt odors that may indicate a problem.
- Examine the Power Cord: A damaged power cord can interrupt electricity flow, stopping the ice maker from working. If you notice any frays or cuts, consider replacing the cord.
- Check Underlying Wiring: Internal wiring issues within the refrigerator or freezer could hinder the ice maker's power supply. Inspect these parts if you're comfortable, or schedule an appliance repair professional.
- Test for Electrical Codes: Keep an eye out for flashing codes on your refrigerator or freezer. These can indicate electrical faults that need addressing.
By addressing power supply problems early, you help keep your ice maker producing ice effectively. If these inspections do not resolve the issue, other parts like the ice maker's components or water supply might be at fault. For in-depth guidance on similar issues, consider reading about troubleshooting your ice maker.
Addressing Water Supply Problems
Resolving Issues with Water Flow to Enhance Ice Production
A consistent water supply is crucial for your GE Profile ice maker to function efficiently. If you notice your appliance isn't producing ice cubes as it should, checking the water supply might just be the solution. Here are some essential steps to help you assess and address water supply problems:
- Inspect the Water Valve: Your ice maker relies heavily on the water inlet valve, which controls the flow of water into the maker. If it's malfunctioning, it could impede the appliance's ability to produce ice. Ensure the valve is open fully and not obstructed.
- Assess the Water Filter: A clogged or outdated water filter can disrupt the flow of water, decreasing ice production. Check the condition of your water filter and replace it if necessary. It’s recommended to change the filter every six months to maintain optimal performance.
- Examine the Water Line: Ensure that the water line connected to your refrigerator freezer is not kinked or damaged. Accidental damage could restrict water flow, affecting the ice maker's functionality.
- Temperature Regulations: The temperature settings of your freezer also play a critical role. If the freezer is too warm, it might prevent the water from freezing into ice. Verify and adjust the temperature settings to help keep your ice maker working efficiently. Learn more about optimizing ice production here.
If these checks don't resolve the issue, it might be time to consider checking other components or scheduling a service with an appliance repair professional. Be sure to explore other reasons why your ice maker issues occur, as understanding the root cause can save you both time and unnecessary repairs.
Mechanical Failures and Component Checks
Inspecting the Mechanical Components
When tackling mechanical issues in your GE Profile ice maker, begin by checking the appliance's internal parts. Mechanical failures can significantly impact ice production, causing the unit to stop making ice. Here's how you can proceed:- Examine the Ice Bin: Sometimes, the ice bin may not be properly seated, preventing ice from being dispensed. Ensure the bin sits correctly in its position within the refrigerator freezer, as misalignment can halt operations.
- Check the Inlet Valve: The water inlet valve is vital for supplying water to the unit. Inspect it for any blockages that could restrict water flow, and ensure it is receiving power. If the valve is defective, ice makers won't be able to produce ice.
- Verify the Control Board: The control board manages the ice-making cycle. Malfunctions here can stop the maker from working. If you suspect the board is damaged, consider seeking appliance repair help for this complex part. Delicate repairs may be necessary to restore full function.
- Look into Water Filter Issues: A clogged water filter can impede water flow to your ice maker, affecting ice production. Replace the filter regularly to maintain optimal performance and help keep the maker working efficiently.
- Check for Ice Blockages: Sometimes, ice clogs can develop within the dispensing chute. If you find that ice cubes aren't being released properly, clear any obstruction or jammed ice from the area to restore normal operation.
When to Call a Professional
Recognizing When Professional Assistance is Needed
Sometimes, despite your best efforts in troubleshooting the GE Profile ice maker, the issue might remain unresolved. Identifying when it's time to seek professional appliance repair services is crucial to avoid further damage to parts, such as the control board, inlet valve, and other vital components. Firstly, if you have diligently checked the power supply and addressed any water supply problems, yet your ice maker is still not making ice or the ice cubes produced are irregular, it may be an indication of more complex mechanical failures. At this point, professional technicians have the expertise to accurately diagnose issues that might not be apparent to an untrained eye. Moreover, if there are any unusual codes appearing on your refrigerator's display panel, or if the refrigerator freezer continues to remain at an inappropriate temperature despite adjustments, these are also signs that professional help may be needed. Technicians equipped with the right tools can thoroughly inspect your appliance, check each part, and execute the necessary repairs to get your ice maker working efficiently again. Lastly, in situations where components such as the water inlet valve or water filter need replacing, having a professional service the refrigerator ensures proper installation and functionality. A professional can not only replace these parts but further assist in performing a complete bin and freezer repair, ensuring optimal ice production and quality. In summary, while basic troubleshooting can often resolve common issues, the longevity of your GE Profile ice maker may depend on timely and qualified repair services when the situation demands it.Preventive Maintenance Tips for Your GE Profile Ice Maker
Simple Practices to Enhance Longevity
Maintaining your GE Profile ice maker is crucial for its longevity and efficiency. Regular upkeep can help keep your appliance at peak performance and prevent issues like the ice maker not working effectively or producing less ice.
Regular Cleaning Routines
- Empty and clean the ice bin regularly. This prevents mold and unpleasant odors.
- Use a soft cloth and mild detergent to wipe down the interior of the ice maker, avoiding abrasive materials that can damage parts.
- Check the water filter monthly. Replacing it when necessary ensures clean ice production and optimal water pressure.
Optimal Temperature Settings
- Ensure that your refrigerator freezer is set to the correct temperature. A freezer that is too warm can hinder ice production.
- Keep the freezer at a constant temperature of approximately 0°F (-18°C) for best results.
Inspecting Key Components
- Regularly check the water inlet valve for any leaks or obstructions.
- Inspect the ice maker's electrical connections and the control board for any visible damage or loose parts.
Scheduling Routine Service
- It's advisable to schedule annual appliance repair services to catch any potential problems early.
- A professional can provide thorough inspections, ensure all components are working properly, and make necessary repairs.