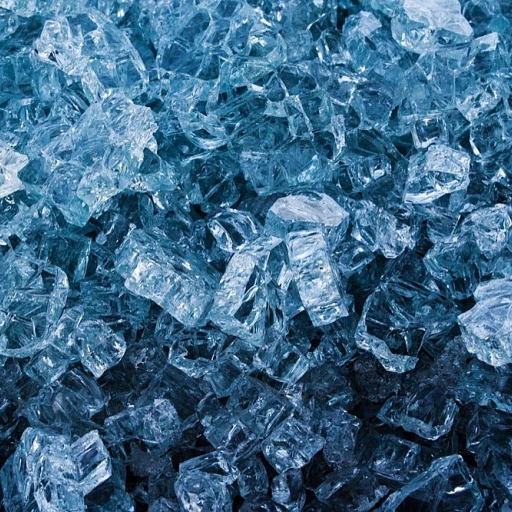
Understanding Common Ice Machine Issues
Troublesome Symptoms of Ice Machines
Running a successful business often relies on a dependable commercial ice maker. However, ice machines can experience a variety of issues that can disrupt your operations. Recognizing these problems early can prevent major disruptions and more costly repairs down the line.
Recognizing Water-Related Problems
Water quality and supply issues are frequent culprits in ice production failures. A Frigidaire ice maker can offer insights into prevalent problems such as inadequate water supply or mineral buildup. Regular cleaning and maintenance of water filters and supply lines are essential preventative measures to ensure continuous and efficient ice production in commercial environments.
Comprehensive Understanding of Appliance Wear
As with any appliance, commercial ice machines are susceptible to wear and tear over time. Components like motors, pumps, and sensors may fail due to extensive use, impacting ice production and machine performance. Routine machine maintenance can help diagnose these issues before they cause significant downtime. Additionally, partnering with a qualified appliance repair technician can ensure that any wear-related problems are addressed promptly.
Tackling Refrigeration System Malfunctions
Refrigeration issues can also impact the ice-making process. A malfunctioning refrigeration unit may result in underperforming ice makers, leading to insufficient ice production. Inspecting and adjusting the refrigeration system's settings and components regularly can prevent and address potential problems and keep your ice machines functioning optimally.
By understanding and addressing these common ice machine challenges, businesses can maintain seamless operations and prolong the life of their equipment. Whether opting for DIY solutions or seeking professional repair services, it’s crucial to be proactive rather than reactive in managing your commercial ice-making equipment.
Essential Maintenance Tips for Longevity
Routine Care Practices for Your Ice Machines
Commercial ice makers are pivotal for any business that relies on ice production, be it a bustling bar or a cozy café. Implementing routine maintenance can significantly extend the life of your ice machines, ultimately safeguarding your investment and ensuring consistent operation.
Regular CleaningA clean ice maker doesn't just enhance the quality of the ice it produces; it also ensures the machine's efficiency. Over time, water deposits can accumulate, causing scaling and reducing the effectiveness of the equipment. It's essential to clean the appliance thoroughly, using appropriate cleaning solutions specifically designed for ice machines. Both the interior and exterior surfaces of the machine should be included in this cleaning regimen. Consistent cleaning not only supports optimal performance but also helps in pinpointing potential issues early on.
Water Filtration and QualityThe water used in the ice making process directly affects the machine's functionality and the quality of the ice. Regularly changing the water filter is critical. This simple service act reduces impurities and maintains the ice's taste and clarity. Additionally, hard water can lead to more frequent maintenance repair due to scale build-up. Using a water filtration system can effectively mitigate this problem, ensuring smooth and efficient ice production.
Check the Stroke Width and Other ComponentsMonitoring and adjusting the stroke width and other mechanical components of the ice machine will keep it running smoothly. This involves ensuring that the machine's fill and stroke settings are optimized for the best ice production capability. Regular inspections of these components can preempt machine repair issues and keep the machines operating at peak efficiency.
Invest in Preventative MaintenanceThough it might be tempting to wait until issues arise before seeking repair services, proactive maintenance is a more sustainable approach. Investing in a preventative maintenance plan with a reliable service repair company can save you unforeseen expenses by catching problems before they escalate into costly commercial ice machine issues.
For more detailed troubleshooting information and maintenance repair tips, click here for typical ice machine solutions.
DIY Troubleshooting Techniques
Common Techniques to Tackle Ice Maker Problems
For businesses that rely on ice machines, encountering malfunctions can be disruptive. Fortunately, many issues can be resolved with simple troubleshooting methods. Here's a straightforward guide to help you address these common appliance nuisances before seeking commercial repair services.- Assess the Water Supply: The first step in troubleshooting ice makers often involves examining the water source. Ensure that the water line is properly connected and that valves are open. A clogged filter could also impact water flow, so regular cleaning and maintenance are essential to maintain efficiency.
- Inspect Ice Machine Components: Ice makers have various internal components that may need attention. Check for any loose connections or faulty parts that might need repair. If the ice production has stopped or decreased, these inspections can quickly highlight the root of the problem.
- Consider Refrigeration Needs: Ensure that your refrigeration system is functioning correctly. Any deviation in the temperature settings could affect ice machine performance. Adjust settings if necessary to ensure optimal ice production.
- Evaluate Cleaning Procedures: Cleaning is crucial for preventing breakdowns. Mineral buildup and debris can cause blockages, so follow manufacturer guidelines for cleaning and preventative maintenance. This simple step keeps your appliance in top condition and prolongs its service life.
When to Call a Professional Technician
Identifying When Expert Assistance is Necessary
When you're dealing with ice machine repairs, there comes a point when calling in a professional technician isn't just advisable—it's essential. Recognizing these moments can save your commercial ice maker from further damage and ensure that your business operations continue smoothly.- Unusual Noises: If your ice machine starts making grinding or clicking sounds, it might be experiencing mechanical issues that require a trained ear. Such noises are often symptomatic of more significant problems within the equipment, like worn-out components or improper water flow.
- Consistent Leaks or Water Supply Problems: Persistent leaks or water fill problems usually indicate issues with the appliance's internal tubing or valves. These issues can lead to inefficiencies in ice production and may necessitate expert intervention.
- Ineffective Ice Production: When essential maintenance efforts don't resolve production shortcomings, a technician's expertise can quickly identify and repair the underlying causes. They have the tools to address everything from clogged filters to refrigeration malfunctions effectively.
- Electrical Malfunctions: Whenever an ice maker encounters electrical issues, such as circuit failures or control panel malfunctioning, seek professional help for appliance repair. Addressing electrical problems without expertise poses safety risks and could lead to further damage.
- Stopped Operation: If your commercial ice maker abruptly stops working despite regular maintenance and DIY troubleshooting attempts, it is time to engage a skilled service. Abrupt stoppages often indicate severe internal breakdowns that require professional repairs.
Choosing the Right Repair Service
Evaluating Repair Services for Your Ice Machine
Choosing the right repair service for your commercial ice machine is crucial to ensure efficient and lasting solutions. With a variety of options available, it's important to consider several factors before making a decision. Here are some key points to keep in mind:
- Experience and Expertise: Look for repair services with a proven track record in handling commercial ice machines. Experienced technicians will be more adept at diagnosing and fixing issues efficiently.
- Comprehensive Services: Opt for a service provider that offers a wide range of services, from routine maintenance to complex repairs. This ensures that all your needs are met under one roof, saving you time and hassle.
- Availability and Response Time: In a business setting, time is money. Choose a repair service that offers prompt response times and is available for emergency repairs to minimize downtime.
- Reputation and Reviews: Check online reviews and testimonials to gauge the reliability and quality of the service. A company with positive feedback is more likely to deliver satisfactory results.
- Cost-Effectiveness: While cost shouldn't be the only factor, it's important to find a service that offers competitive pricing without compromising on quality. Consider requesting quotes from multiple providers to compare.
- Warranty and Guarantees: A reputable repair service will stand by their work, offering warranties or guarantees on parts and labor. This provides peace of mind and assurance of quality workmanship.
By carefully evaluating these aspects, you can select a repair service that not only addresses your immediate needs but also contributes to the long-term performance and reliability of your ice machines. Remember, regular maintenance and timely repairs are essential to prevent recurring issues and ensure optimal ice production for your business.
Cost-Effective Repair Strategies
Maximizing Value with Smart Repair Choices
When it comes to repairing your commercial ice machine, cost-effectiveness is key. Balancing quality and budget can be challenging, but with the right approach, you can ensure your ice maker is back in top shape without breaking the bank.
- Preventative Maintenance: Regular maintenance is crucial. By keeping up with routine cleaning and machine maintenance, you can prevent costly breakdowns. This proactive approach not only extends the life of your equipment but also reduces the need for frequent repairs.
- DIY Solutions: Before calling in the professionals, try some DIY troubleshooting techniques. Simple fixes like checking the water fill levels or ensuring the appliance is properly plugged in can sometimes resolve minor issues.
- Professional Services: When professional help is needed, choose a repair service that offers competitive pricing and reliable service repair. Request quotes from multiple repair services to compare costs and services offered.
- Warranty Considerations: Check if your ice machine is still under warranty. If so, repairs might be covered, saving you significant expenses.
- Long-Term Savings: Investing in quality repairs and maintenance can save money in the long run. A well-maintained commercial ice machine will operate efficiently, reducing energy costs and minimizing downtime for your business.
By following these strategies, you can manage your ice machine repair costs effectively while ensuring your ice production remains consistent and reliable.